The landscape of construction and building safety has undergone significant transformations over the years, with channel systems playing a critical role in the development and integrity of modern infrastructure. The journey from untested channel systems to the sophisticated, tested channels of today, and the emerging future of automated design tools, reflects a broader evolution in building safety and compliance.
- The Past: Traditional Channel
- The Pitfalls of Untested Channel
- The Shift Towards Tested Channel Systems
- The Present: Tested Channel Systems
- The Future: Automated Design Tools
- Introducing dynaMX®: A Leap Forward in Bracket Configuration
- Conclusion
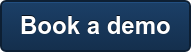
The Past: Traditional Channel
Channel systems, coupled with threaded rods and associated fixings, offer a versatile solution for supporting and organising various building services. They can be prefabricated into support frames to accommodate single-pipe, double-pipe, or cable runs. These setups can range from simple, single-tiered trapeze brackets to more complex, multi-tiered configurations suspended from metal decking or anchored directly into concrete substrates. The flexibility of these systems allows for tailored solutions that can be adapted to the specific needs of a project.
The Pitfalls of Untested Channel
The main issue with untested channel assemblies lies in the ad hoc nature of their assembly and installation. In the M&E sector, there is a tendency to mix and match products from different systems without adequate testing to verify their compatibility or overall performance when used together. This approach is problematic for several reasons:
- Lack of Systemisation: Without testing, these components are merely individual products rather than parts of a cohesive system. There's no verified data to prove how they will perform under various conditions or over time, making it difficult to predict their reliability and safety.
- Safety and Performance Risks: The absence of testing means that the ability of these assembled supports to bear loads, resist environmental stressors, and maintain structural integrity over the lifespan of the building is uncertain. This uncertainty poses risks not only to the building's infrastructure but also to its occupants.
- Procurement and Installation Practices: The Building Engineering Services Association (BESA) highlights in its 'Guide to Good Practice for Supports and Fixings' (TR50) that procurement decisions are often made based solely on price, without considering quality or compatibility. Additionally, changes to these systems are frequently made on-site without understanding the implications, further exacerbating the risk of failure.
- Regulatory and Compliance Issues: With the introduction of stricter building regulations, such as those outlined in the Building Safety Act 2022, the lack of testing and systemisation in channel systems can lead to compliance issues, legal ramifications, and the need for costly remediation work.
The Shift Towards Tested Channel Systems
The transition to tested channel systems in the construction industry marks a significant shift towards prioritising safety, reliability, and compliance. This change can be understood as a multifaceted process, influenced by technological advancements, regulatory pressures, and a growing recognition of the need for empirical evidence to support the use of construction materials and methods. Let's delve deeper into the key factors that catalysed this transition and its implications.
Increased Complexity of Modern Structures: As architectural designs and construction projects became more ambitious and complex, the limitations of traditional, untested channel systems became evident. The demand for taller, larger, and more innovative structures, otherwise known as high-risk buildings (HRBs), necessitated a more rigorous approach to material and system selection.
Historical Failures and Safety Concerns: High-profile structural failures and safety incidents highlighted the dire consequences of inadequate material testing. The Grenfell Tower tragedy in 2017 exemplifies the devastating consequences of neglecting the safety and testing of building materials and systems. It led to a re-evaluation of construction practices worldwide, emphasising the need for stringent testing, certification, and compliance to prevent such disasters in the future.
Regulatory and Industry Standards: The Grenfell Tower fire served as a wake-up call, highlighting the dangers of untested or inadequately tested building materials. In the aftermath, there was a significant push for stricter regulations and standards in building materials and construction practices. The tragedy played a pivotal role in the development and enforcement of the Building Safety Act 2022, which aims to improve building safety standards across the UK. This act underscored the importance of using tested channel systems by setting stringent standards for safety and performance. This act not only aimed to prevent accidents and failures but also to instill a culture of safety and accountability within the industry. By setting clear guidelines and standards, it provided a regulatory framework that supported the shift towards universally tested and verified channel systems.
One of the primary requirements of the Building Safety Act 2022 is the need for evidence through rigorous testing and certification to back up all building installations. This necessitated that support systems be tested as complete units to confirm their load capacity and suitability for intended use. Merely depending on the manufacturer's data for individual components no longer sufficed as adequate proof of their overall effectiveness and reliability.
This gave rise to the popularity of tested channel systems.
The Present: Tested Channel Systems
Tested channel systems are essentially support frameworks that have been rigorously tested to confirm they adhere to certain standards of strength, durability, and safety. To achieve an effective tested channel system, it is essential to focus on two key elements.
First, the system must undergo comprehensive testing at an independent facility. This testing goes beyond simply inspecting individual components; it involves a thorough evaluation of how component connections assemble across a variety of standard configurations. Such a methodical approach produces reliable load data, which is crucial for engineers. This data helps them design supports that ensure the structural integrity and optimal performance of the installation, affirming its safety and effectiveness.
Second, it's imperative that all system components are easily identifiable, each marked with the manufacturer's name or logo. This level of traceability verifies that the components are part of a cohesive system that has been tested and certified to work together safely. It also facilitates the verification process, confirming that the system has been implemented correctly and that all parts are tested and validated as a unified entity.
Ultimately, a well-tested channel system provides robust evidence that your bracket assembly is suitable for its intended purpose. It guarantees compliance with safety standards, including those outlined in the Building Safety Act 2022. By ensuring your channel systems meet these standards, you safeguard against financial and reputational damage and, most importantly, prevent onsite safety risks associated with bracket suspension failures.
The Future: Automated Design Tools
Looking ahead, the evolution of tested channel systems is poised to embrace the potential of automation and advanced technology. Automated design tools represent the next frontier, promising to revolutionise the way channel systems are used to create common repeatable brackets like trapezes and AHU frames. These tools leverage algorithms to optimise designs, predict performance under various scenarios, and identify potential issues before installation. This not only accelerates the design process but also enhances the precision and reliability of channel systems.
Tested channel systems are ideally suited for automation for several reasons, rooted in the comprehensive testing these systems undergo and the precise, reliable data they provide. Here's why they make a perfect match for design automation tools or online configurators:
- Reliable Data Foundation: Tested channel systems undergo extensive testing, ensuring each component's performance is well-documented and understood. This wealth of data provides a solid foundation for automation tools, enabling accurate simulations and predictions of how the systems will perform in various scenarios. By leveraging this data, automation tools can ensure bracket designs meet the necessary safety and performance standards.
- Consistency and Standardisation: The rigorous testing protocols for channel systems result in consistent and standardised product specifications. This uniformity is ideal for automation, as it allows for the development of algorithms that can reliably predict outcomes based on a set of standard inputs. Automation thrives on consistency, which tested channel systems readily provide.
- Optimal Design Outcomes: Using data from tested channel systems allows automation tools to achieve optimal design outcomes. Since the performance characteristics of the components are well understood, these tools can more accurately calculate the best configurations for specific requirements. This ensures that designs are not only compliant with safety standards but also optimised for efficiency and cost-effectiveness.
- Efficiency in Repetitive Designs: For repetitive design tasks, such as configuring supports for pipes and cables, automation can significantly increase efficiency. Instead of applying a one-size-fits-all approach, automation tools can tailor designs to each specific application, taking into account the unique requirements of each project. This leads to more precise and effective designs, reducing waste and improving overall project outcomes.
- Scalability and Speed: Automated design tools can process a vast amount of data and generate multiple design solutions quickly, far surpassing the capabilities of manual design processes. This speed and scalability make automation particularly appealing for projects with repetitive elements or those requiring rapid turnaround times.
In summary, the inherent reliability, consistency, and depth of data provided by tested channel systems make them perfectly suited for integration with automation technologies. This combination enhances design accuracy, efficiency, and innovation, ultimately leading to safer, more efficient, and cost-effective construction projects.
But why should we automate the design process for tested channel systems?
- Increased Efficiency and Productivity
Automated design tools streamline the design process by significantly reducing the time and effort required to create and modify designs. An online bracket configurator, for example, can instantly generate bracket designs based on specific inputs, eliminating the need for manual calculations and drawings. This efficiency boost not only accelerates the design phase but also allows engineers and designers to focus on more complex tasks, thereby increasing overall productivity.
- Enhanced Accuracy and Consistency
Human error is a common issue in manual design processes. Automated tools minimise this risk by ensuring that designs are generated based on precise mathematical models and algorithms. This leads to higher accuracy and consistency in the products designed, reducing the likelihood of errors that could result in product failures or safety issues. An online bracket configurator would ensure that every design adheres to the specified parameters, eliminating variations that could affect the end product's performance.
- Customisation and Flexibility
One of the standout advantages of automating design tools is the ability to easily customise products to meet specific customer requirements. An online bracket configurator allows users to input their own specifications, such as dimensions, materials, and load requirements, to create a product that perfectly fits their needs. This level of customisation enhances customer satisfaction and can give companies a competitive edge in the market.
- Rapid Prototyping and Testing
Automated design tools can enable professionals to test and analyse the performance of their designs under various conditions without the need for physical prototypes. This capability not only saves time and resources but also allows for the optimisation of designs before they go into production. With an online bracket configurator, for instance, users can quickly iterate on designs and assess their viability, making it easier to refine and improve products.
- Cost Reduction
The automation of the design process can lead to significant cost savings. By reducing the time spent on designing, the need for physical prototypes, and the risk of errors, companies can lower their overall development costs. Furthermore, the ability to precisely customise products reduces waste and ensures that resources are used more efficiently.
- Accessibility and Ease of Use
Automated design tools, especially those available online, can be accessed from anywhere, at any time. This accessibility makes it easier for teams to collaborate on projects, regardless of their physical location. Moreover, these tools are often designed with user-friendly interfaces, making them accessible to professionals with varying levels of technical expertise.
- Streamlined Documentation for Regulatory Approval
Obtaining regulatory approval often requires extensive documentation of the design process, including how safety and compliance were addressed. Automated design tools can generate detailed reports and documentation, providing a clear audit trail from initial design to final product. This documentation is essential for demonstrating compliance to regulatory bodies and can significantly streamline the approval process.
In summary, automating design tools like a bracket configurator bring transformative benefits to the design and manufacturing process. These tools enhance efficiency, accuracy, and customisation, while also providing cost savings and improving market responsiveness. As technology continues to advance, the adoption of such tools is becoming increasingly essential for companies looking to innovate and excel in their respective industries.
Introducing dynaMX®: The Future of Bracket Configuration
Building on the transformative benefits of automating design tools, which enhance efficiency, accuracy, customisation, and ensure safety and compliance, MIDFIX introduces its cutting-edge solution: dynaMX®.
dynaMX® is an innovative online bracket configurator developed to meet the specific needs of the construction industry, particularly focusing on M&E applications. This platform marks a significant departure from traditional bracket configuration methods, embracing advanced algorithms and customisable design options to automate the bracket configuration process of simple, repeatable designs such as trapeze frames.
By allowing users to input a wide array of project specifications, such as load requirements, substrate preferences, and spacing constraints, dynaMX® can automatically generate optimised bracket configurations in a matter of a few minutes and a fraction of the cost. Automated load and stress analysis ensure compliance with regulations, supported by comprehensive configuration reports. This greatly reduced the risk of human errors, which can have adverse consequences in the case of safety-critical M&E applications, thereby enhancing overall project efficiency, safety and reliability. The platform also allows for futureproofing by incorporating additional design capacity. Importantly, dynaMX® is accessible for free, aiming to support the construction industry by providing advanced design tools without financial commitment.
dynaMX® has been meticulously designed to work specifically with the components and load requirements MIDFIX MX Channel System. This ensures that users benefit from designs that are not only optimised but fully compliant with the specifications and performance standards of a trusted channel system.
Conclusion
The evolution of channel systems, from their untested beginnings to the rigorously tested configurations of today, and the forward leap towards automation, encapsulates a significant shift in the construction and building safety landscape. This transformation has been driven by the need for greater reliability, efficiency, and compliance in the face of increasingly complex construction demands and stringent safety regulations.
As we look towards the future, the role of automated design tools, such as dynaMX®, becomes increasingly central. dynaMX® represents the culmination of this evolutionary journey, offering a sophisticated solution that leverages the benefits of automation to enhance design efficiency, accuracy, customisation, and compliance. By automating the design process, dynaMX® not only streamlines the creation of optimised bracket configurations but also ensures that these configurations are aligned with the rigorous standards set forth by modern safety regulations and the specific requirements of the MIDFIX MX Channel System.
This evolution from untested to tested, and now to automated design tools, reflects a broader trend towards embracing technology to meet the challenges of modern construction. It underscores the industry's commitment to safety, efficiency, and innovation. As automated tools like dynaMX® become more integrated into the design and construction process, they promise to further elevate the standards of building safety and compliance, ensuring that the construction industry can meet the demands of today and the challenges of tomorrow with confidence and precision.