As part of our goal to help guide and educate the industry we have started a series of podcasts, the premise is simple, we want to help solve the common issues which the sector face. We hope to achieve this by interviewing a series of experienced experts within their given field.
In our first podcast we aim to guide the industry with anchor/fixing compliance by interviewing one of the oldest manufacturers of fixings, RawlPlug.
By the end of this blog you will have an overview and an answer to the following questions, feel free to jump to the relevant section.
BS 8539:2012 overview
Key points from BS 8539:2012
Why was BS 8539:2012 Code of Practice introduced?
Who does BS 8539:2012 affect?
How does BS 8539 affect designers, specifiers, contractors, installers, site testers, manufacturers, and suppliers?
When selecting an anchor, what factors should be considered?
Understanding substrates
How does BS 8539:2012 differentiate between cracked and non-cracked concrete?
How does BS 8539 guide the specifier to understand the load rating when selecting an anchor?
What role does the environment surrounding an anchor play in selecting an anchor?
What are the working principles of an anchor/fixing?
What type of approvals should be considered when selecting an anchor?
What should a supplier offer?
Can you change the specified anchor to another of similar size and description?
How does the BS 8539:2012 affect the installer?
Why do anchors/fixings fail?
How can you provide evidence of a compliant anchor/fixing installation?
How does BS 8539:2012 code of practice guide on-site testing?
How does a subcontractor provide evidence of a compliant anchor/fixing installation?
Before a proof test is carried out onsite, what type of information do you require?
What is an anchor/fixing policy?
Why is a fixing policy important?
How can we change the perception of anchors/fixings?
BS 8539:2012 impacts every stakeholder involved in the selection, supply, installation, and testing of anchors
In this podcast we catch up with Peter Gordan from RawlPlug UK to discuss the impact of BS 8539:2012. He discusses the standard and offers practical advice for designers, specifier, distributors, suppliers, main contractors, installers and trainers.
Looking for a complete overview of anchor/fixing compliance?
What is BS 8539:2012 Code of Practice for post-installed anchors for concrete and masonry?
The BS (British Standard) 8539 was published in 2012, adapted and driven forward by the CFA, setting out a standard procedure for the safe selection, supply, installation, and testing of anchors/fixings installed in concrete or masonry.
The purpose of the BS 8539:2012 is to guide designers, specifiers, manufacturers, suppliers, contractors, installers, and testers of anchors, to ensure a safe and compliant install. BS 8539 refers to ETA (European Technical Assessment) and recommends specifying anchors within the correct ETA for the given application.
Furthermore, the BS 8539:2012 states that as soon as an individual takes responsibility for selecting the anchor, they immediately become the specifier and therefore liable for any consequential errors.
In reference to the BS 8539, the CFA highlights the following:
“If fully adopted, it will result in a reduction of failures of construction fixings with consequent savings in injuries, deaths, and liabilities.” (CFA, 2015)
Key points from BS 8539:2012
- ETA-approved anchors should be used where available.
- The correct anchor must be sourced as specified. If an alternative anchor is proposed, the change management procedure must be followed.
- Installers must be competent with the anchor installation. They must be supervised and upon completion, the installation should be certified by the contractor’s supervisor.
- Site tests in accordance with the CFA guidance notes should be undertaken by a competent tester.
Why was BS 8539:2012 code of practice introduced?
As Peter explains, "BS 8539 was an adaption of an Irish standard which was brought out after a major fatality onsite”. Some key issues within the construction industry highlighted the need for a British Standard:
- Specification changes for practical and commercial reasons.
- There was no set procedure for stakeholders to follow for installing an anchor.
- Tests were often carried out by the manufacturer in-house, with no independent verification leading to inaccurate design specification and loading information.
- Over 80% of drop-in anchors are installed incorrectly.
Who does BS 8539:2012 affect?
The British Standard sets out a step-by-step process involving all stakeholders, including:
- Designer
- Specifier
- Contractor
- Installer
- Site tester
- Manufacturer
- Supplier
Peter goes onto explain, “Every stakeholder has a part to play in the process of BS 8539:2012. It gives you traceability and a set responsibility within the structure, which means that the end game is to have a safe installation using the correct anchor, as designed and installed to the manufacturer’s guideline.”
How does BS 8539 affect designers, specifiers, contractors, installers, site testers, manufacturers, and suppliers?
We have created a handy table summarising how the BS 8539 guides all of the stakeholders;
Role | What BS 8539 states |
---|---|
Designers
Design the complete building which means they have access to all of the information incl. load rating and the substrate. In the M&E industry it is very rare that the designer is the specifier. |
The designer should outline the anchor/fixing, drawing on the manufacturer’s description and part code so that the supplier can select the correct anchor. When selecting an anchor, the following should be considered (which we will go into in more detail later): · The substrate that the anchor is being fixed into; cracked/uncracked concrete, block, brick, timber etc. (Clause 5) · Can the anchor sustain the load bearing of the application? · Environment of the anchor. Will it be outside, inside, humid or not and what finish is suitable? From carbon steel to zinc-plated to stainless steel, to high corrosion resistant materials. · Type of installation – flush-fixed or through fixing. · Type of anchor - torque-controlled, deformation-controlled, undercut or resin. · Approvals - does the anchor meet the ETA approval? |
Specifiers
According to BS 8539, any individual within the supply chain of an anchor can be referred to as a ‘specifier’. They select the anchor/fixing. |
· The make, type, ETA number, size and manufacturer reference/order number. · Instructions for installation. · Guidance for the installer on what to do if reinforcement is hit when drilling. |
Contractor
Employs the installers onsite. It is their responsibility to ensure installers are trained. |
The contractor should provide the correct anchor as specified. If changing this specification, they should carry out the due diligence to ensure that clause 10 of the change of management procedure is followed. If the contractor has seen that the anchor specified is not the correct one, they should inform the original specifier. The contractor should install the anchor to the manufacturer’s specifications (or training). |
Manufacturer
Those that manufacture the anchor/fixing. |
The manufacturer should provide: · All information for the specifier to select the correct anchor. · Technical catalogues and software. · Installation instructions for the installer. · Recommended resistance (or appropriate safety factor to allow calculation). · Setting details including min. thickness of base material, edge and spacing criteria. · Installation instructions and equipment needed. |
Supplier
Those that supply the anchor on site |
The supplier should provide: · Provide the anchor as specified, unless a specific change management procedure has · Take the opportunity to ensure all associated setting equipment is offered to the contractor such as drill bits, hole cleaning equipment, setting tools, torque wrench etc., so that the installer can install anchors correctly. · Provide installation training or facilitate this being provided by the manufacturer. · Provide guidance in anchor selection. · Ensure the change management procedure is adhered to if asked for alternatives. |
Supervisors Individuals that supervise a fixing/anchor install into a substrate onsite |
The supervisor is responsible for signing off an anchor installation prior to the anchor being loaded: · They should be adequately trained. · They are responsible for insuring the specified anchor is the actual anchor being installed. · They carry out the final check after installation. · They make sure the installation is done correctly. |
Installers Individuals that install a fixing/anchor into a substrate onsite |
BS 8539:2012 states that anchors should be installed and supervised by competent individuals. BS 8539 defines competent as:
“Suitably trained and qualified by knowledge and practical experience, and provided with the necessary instructions, to enable the required task(s) to be carried out correctly”. When the anchor is originally supplied to site, the installer should look at the setting tools (e.g. torque wrench, torque specification and set the torque up correctly). The drill diameter, drill depth, recommended torque value and load bearing should also be taken into consideration. |
Site testers Usually a manufacturer or distributor that tests the anchor after installation, as requested by the contractor. |
BS 8539:2012 states that testing is not required if an ETA anchor has been used, installed and supervised by competent individuals. This means: · Anybody carrying out a site test should be qualified by the CFA. · Proof testing or allowable load testing CFA guidelines should be followed. · Correct reporting procedures as per CFA guidelines should be followed. |
When selecting an anchor, what factors should be considered?
- Substrate - the manufacturer should advise what substrate is suitable for that anchor, cracked or non-cracked concrete.
- Loadings - what load can the fixing take and can the fixing perform to the load requirement? Once again, this would be outlined by the ETA.
- Environment – is it a corrosive environment?
- Type of install – is it going to be a through fix or a flush fix?
- Type of anchorage – torque-controlled, deformation-controlled, undercut/key or resin.
- Approvals - ETA documentation.
Understanding substrates
- Concrete – cracked or non-cracked.
- Brick - solid or hollow.
- Blockwork is becoming lighter and we are hanging heavier loads on them.
- Steel Decking is quite common onsite. If we cannot fix steel decking to the entrant where a lindapter wedge would fit, then we need to drill into the substrate.
How does BS 8539:2012 differentiate between cracked and non-cracked concrete?
Anchors that are qualified to be used with cracked concrete are expected to function reliably, in the expected widths of cracks developed. This is a result of tensile stresses in concrete structures, designed in accordance with BS EN 1992. In the region of an anchor, the concrete might be cracked or non-cracked.
According to the BS8539, you have to assume its cracked unless you can prove otherwise. That’s usually via the structural engineer onsite.
“Cracked concrete can have a 30% decrease in load performance over uncracked concrete. If an anchor is fixed into a substrate it wasn’t designed for, the performance of the anchor can decrease by up to 80%.”
The ETA also looks at cracked and non-cracked approvals, with options 1 to 6 covering cracked and 7 to 12 covering non-cracked.
How does BS 8539 guide the specifier to understand the load rating when selecting an anchor?
Once again, it is the responsibility of the specifier to understand the type of load that is being applied to the anchor. Different factors determine the choice of anchor:
- Is it static or dynamic?
- The magnitude of the load.
- The direction (tension and sheer) of the load.
- The duration of the load (specifically what load is applied to the anchor).
What role does the environment surrounding an anchor play in selecting an anchor?
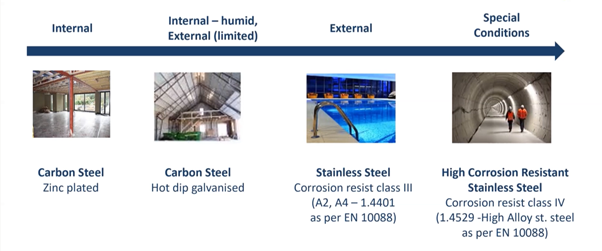
Most internal applications will be zinc plated. For certain applications, for example in a multi-story car park once we remove the walls the environment is altered.
Certain applications such as swimming pools need very careful consideration as the chlorinated environment can induce stress corrosion cracking in some grades of stainless steel.
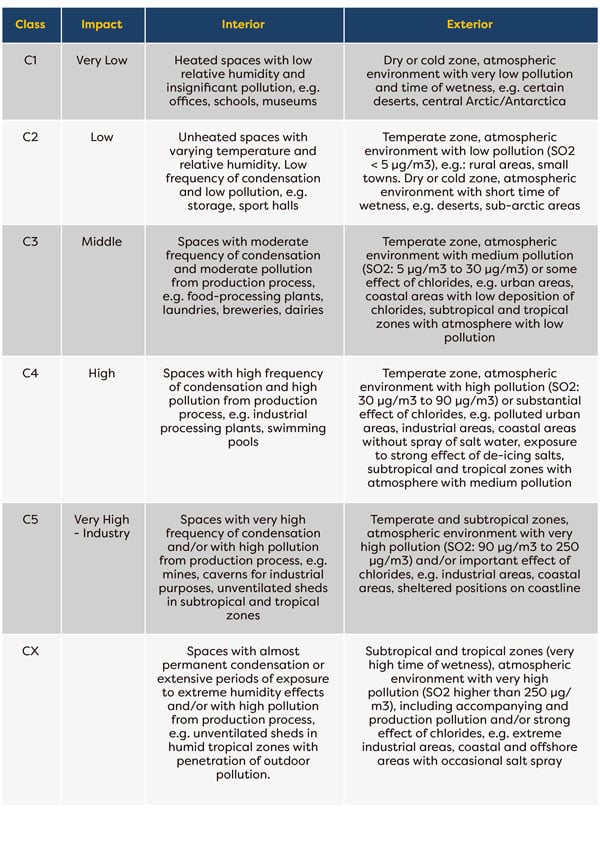
The table above illustrates the different corrosion categories and their impact on different environments as outlined in the ISO 9223 classifications.
What are the working principles of an anchor/fixing?
Flush fix – pre-install anchor into the substrate then apply the fixture afterward.
Through fix – can be fixed straight through the fixture into the substrate for a quicker install but with less accuracy.
The type of installation will determine the suitability of different anchors.
What type of approvals should be considered when selecting an anchor?
BS 8539 recommends only specifying an ETA (European Technical Assessment) anchor. The ETA refers to a harmonised independent set of tests and standards, adhered to by all reputable anchor manufacturers. The ETA is an independent testing house that tests anchors in different substrates and various loads. The ETA document provides performance figures used for the specifier to make the selection. It is awarded following comprehensive testing against a framework, which measures the functionality of the anchors in a wide range of site conditions.
The ETA contains:
- Manufacturer Details
- Product name and intended use
- Manufacturing plant/part number
- Details of the assessment programme and the performance of the product
- The control task of the manufacturer, depending on the relevant AVCP systems
As Peter describes, “ETA is everybody’s guarantee of safety.” From a manufacturer's point of view, if an anchor goes through rigorous testing and the performance data is independent – it is reliable. For contractors, that provides trust as they have all the correct information to hand.
Examples of tests carried out by the ETA include:
- Over-torque the anchor
- Fixing it close to the edge
They then take the mean value of these results and that provides an accurate ETA loading specification.
For a designer or an installer, an ETA verification can help them specify and install the right anchor. There is clear data to refer to. If the installation conditions are as per the ETA test, then that is a guarantee that the fixing will achieve that load value. The ETA supports the quality of the fixing all the way through to the installation.
BS 8539 guidelines outline that the supplier must make the customer aware of the setting tools (or accessories) required for that specific anchor/fixing.
Take a through bolt – the distributor must make a customer aware that they need a torque wrench in order to correctly set the torque of a through bolt. If they do not have a torque wrench, it is impossible to set a through bolt.
There are three types of torque-controlled anchors. The torque is the measure of how the fixing is going to perform. If you over-torque, stress can damage the anchor, and likewise, if you under-torque, it is unlikely you will meet the approved loads outlined within the ETA document.
Is it not good enough to change the specified anchor to another of similar size and description?
This is where the ETA independent tests are vital, as an anchor is tested on one substrate. The guidance recommends that the anchor can only be installed on the application that it has been tested with. For example, cracked or non-cracked concrete.
If there is a fixing change from one that was originally supplied, you need to make sure the new fixing adheres to that standard. As a manufacturer, we will advise and redesign the fixing and therefore, we become liable. Through this process, you ensure customers don’t use fixings in the wrong substrate.
How does the BS 8539:2012 affect the installer?
Installers should be competent in the installation of that anchor type. RawPlug and MIDFIX offer installation training and testing, and now MIDFIX offer online training courses through our own Academy (link). Peter points out that for RawPlug, “Toolbox talks are most effective for installers as it reinforces the correct method of installation. This is because we know most bracketry failures are due to the anchor being installed incorrectly”.
Faulty anchor manufacturing.
Now, in my 35 years I have come across that twice. Fixings are a very simple piece of equipment so the amount of safety built into the design is 4:1. So, if it is the correct anchor in the correct substrate and it’s been installed correctly, it should never fail.
Two of the most common anchor types to fail are:
Resin systems because the chemical/resin anchor has not been cleaned prior, so that is an installation and training issue.
Deformation-controlled anchors - as a manufacturer we do a very simple benchmark – we look at the sale of anchors and the sale of setting tools. If they do not match, you know that an incorrect anchor installation is likely to take place. As mentioned before, for a deformation-controlled anchor you need the specific setting tool for that make and size of anchor.
Why do anchors/fixings fail?
Anchors/fixings very rarely fail due to their in-built design safety factor. However, if a suspension or support collapse occurs on-site it is likely because of two reasons:
1.) It is highly likely that the specifier has not selected the anchor in accordance with the principles outlined in BS 8539.
2.) In the majority of cases anchors/fixings are installed incorrectly because installers have not been given adequate training.
We have written a short guide reviewing the practices that help to mitigate the risk of anchor failure.
Installation of an anchor/fixing is critical; for deformation-controlled anchors, most of them are installed overhead.
The ETA guidelines play a part in aiding installers. Manufacturers of anchors will usually have an indentation mark on them (referred to as a witness mark). Once you install an anchor, it imprints a number of dots on the anchor. Once auditing is carried out on site after installation, we can simply undo the rod and see if the fixing has been installed correctly.
As an example, from a manufacturer’s point of view, if there is a failure on site and you have not used a torque wrench, then you have not installed the fixing under the manufacturer guidelines. Therefore, the installation is not compliant to BS 8539 standard.
How does BS 8539:2012 code of practice guide on-site testing?
Site testing is covered extensively in BS 8539, and the main criteria is the tester needs to be competent. Now, the only competency is through the CFA, so you need to get a qualification through CFA. There are two levels; there is proof testing and allowable load testing.
- Ultimate load testing
- Proof testing
Ultimate load testing
- Testing the substrate is relatively simple to do with lightweight material, but not with more problematic substrates such as a block of beam systems where there is no clear indication of highlighting the capacity of the concrete.
- This is why it is important that while specifying an anchor, you need to know the capacity of substrate that the fixing will be installed into.
- Test the amount of load an anchor can take, working from failure down using safety values.
Proof testing (building insurance companies request proof testing often)
- Has the anchor been installed correctly?
- A manufacturer may be asked to test five anchors/fixings in one substrate, or to test every 1 in 25 or 1 in 40.
- If they are flush-fixed (bolt head anchor) or a frame fixing, you simply can’t test the anchor as you can’t attach it.
Ultimately, a proof test just tests the quality of the installation.
There is further guidance from BS 8539:2012 regarding proof testing and this is also highlighted on the CFA website.
- How many fixings should you proof test?
- What load should you test to? What is the percentage safety factor and what should it be going to?
- If you are testing 1 in 40 fixings, you are only allowed a factor of 1.5 times the applied load. The actual applied load must not exceed the manufacturer’s recommended load.
- If you test 1 in 25 anchors, the guidelines advise the applied load can be 1.25x the specified load requirement from the manufacturer.
Peter states there is a major issue with proof testing:
“It is becoming a bit of a box-ticking exercise or a commercial requirement more than a safe installation issue”
How does a subcontractor provide evidence of a compliant anchor/fixing installation?
If you log onto the CFA website, you can download the right documentation where you can record the anchor the contractor has specified and the installer has installed. It is important that when the anchor is specified in the design, the correct part code is put on the box. Once this is done, anyone can trace the part code back and examine the fixing specification to see if it is different from what was originally specified.
For us (MIDFIX), proof tests are often requested but how important are they?
BS 8539 states that if a specified anchor has an ETA and it has been installed by a competent installer who is supervised, there shouldn’t be a requirement for a proof test. As a manufacturer, we understand that 95% of bracketry failures are caused by incorrect anchor installation. Training installers is a much more important factor, as Peter explains, “if you go onsite and train installers with a toolbox talk and a practical demonstration.”
Before a proof test is carried out onsite, what type of information do you require?
Before we turn up on site to carry out a proof test, we need to know the following:
- How has the anchor been installed? If there aren’t any witness marks on the anchor, it is likely the anchor will fail the proof test.
- What torque wrench has been used?
- What size drill bit has been used?
- Have the correct setting tools been used?
- The load requirement that the engineer has put forward, which we will examine.
- The load requirement compared to the recommended load, which we will check. As long as it doesn’t exceed that, we will carry out a proof test.
- Relevant substrate information.
For BS:8539, we have covered the selection process and what is required within that process, how to get that to the site (supply), and the install. We have also looked at how crucial training is as well as testing. I think those four main points tend to affect most M&E building services contractors. But is there anything else BS:8539 throws up?
The guiding principle of BS:8539 is to try and negate any critical anchor failures. As a manufacturer, RawlPlug is finding that more and more contractors are trying to implement the standard and ensure they have a fixing plan in place. Most anchor failures cause commercial damage rather than fatalities. If you follow the guidelines and put a stringent process in place, anchor failures are less likely to occur. From the designer to the installer, everyone should follow the practical guidance outlined.
The biggest enemy to the BS:8539 and the implementation of the standard across the construction industry is the following phrase:
”I have always used those fixings and I have always done it that way.”
We have got to try and educate the industry to get away from that mentality. Anchors tend not to fail if they have been installed correctly. Safety is built into the design of an anchor and most anchors have a 4:1 safety factor.
What is a fixing policy?
A fixing and anchor policy is a document that sets out the responsibility of each stakeholder involved in either the selection, installation or testing of anchors/fixings.
The fixing policy is a straightforward version of the BS 8539 and is intended to help the contractor, ensure that, when it is filtered down to the site, the following is understood:
- Selection process (how do we select it?)
- Supply (how do we get it supplied?)
- Install (what are we doing about training?)
- Finally, what is our testing programme going to be
If all of those responsible follow their steps then it will lead to a compliant installation and most importantly the M&E contractor will have the evidence to prove that what you have installed is fit for purpose.
Why is a fixing policy important?
Quite simply a fixing policy can save lives because if it is followed correctly then it reduces the chances of suspension failures caused by the incorrect selection or installation of anchors/fixings.
How can we change the perception of anchors/fixings?
In order to change the industry perception of anchors, it is essential that all the stakeholders in the chain work together to promote the awareness of correctly specifying, supplying, installing, and testing anchors.
For RawlPlug (third largest European manufacturer of anchors/fixings), and for a technical supplier of anchors/fixings (MIDFIX), it is our job to promote the importance of anchor installation through education and training. Peter explains, “there is DIN standards for metal structures and DIN standards for concrete structures, but to connect the two together is often left to the contractor or the distributor to advise. That is a strange scenario when you think about how critical it is because anchors hold metal and concrete structures together.”
Both RawlPlug and MIDFIX encourage contractors, designers, suppliers, manufacturers, distributors, installers, and testers to examine BS:8539:2012 and to read the guidance and notes on the CFA website. BS:8539 should be the benchmark of quality for installing anchors. If you follow the due diligence correctly, anchors/fixings should never be a headache again.
…………………………………………………………………
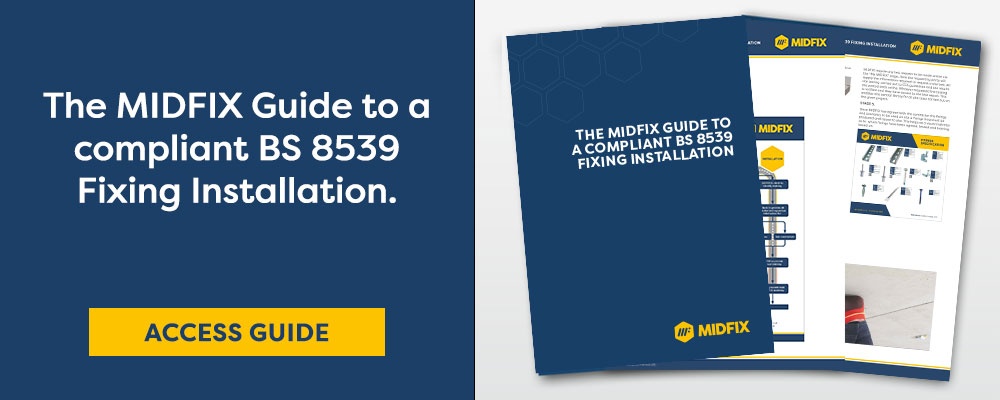
Extra resources
The CFA (Construction Fixings Association) offers a handy online checklist
The CFA website has a wide range of tools designed to guide contractors through the BS:8539. You can also download documentation, guidance, and notes and I would strongly recommend people to do that.
START THE CONVERSATION AROUND ANCHOR/FIXING COMPLIANCE
0115 922 1585
sales@midfix.co.uk
Instantly message our team online (Monday - Friday 7.30am - 5pm)